Inventory Control/Stockroom Clerk III (Lead)
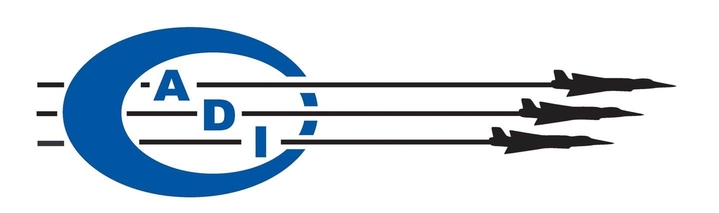
12141
With more than 120 operations and approximately 20,000 employees worldwide, Precision Castparts Corp. is the market leader in manufacturing large, complex structural investment castings, airfoil castings, forged components, aerostructures and highly engineered, critical fasteners for aerospace applications. In addition, we are the leading producer of airfoil castings for the industrial gas turbine market. We also manufacture extruded seamless pipe, fittings, and forgings for power generation and oil & gas applications; commercial and military airframe aerostructures; and metal alloys and other materials for the casting and forging industries. With such critical applications, we insist on quality and dependability – not just in the materials and products we make, but in the people we recruit.
PCC is relentless in its dedication to being a high-quality, low-cost and on-time producer; delivering the highest value to its customers while continually pursuing strategic, profitable growth.
In 2016, Berkshire Hathaway, led by Chairman and CEO Warren E. Buffett, acquired Precision Castparts Corp.
This is a full time on-site position.
Minimum of 2-year experience in Inventory Control required.
Experience as a Lead required.
Position Summary:
Level 3 Inventory Control employees pull kits, issue material out of the ERP system to a job order, and assist assembly personnel with additional hardware requirements. Additionally, work with Production Control Planners for priorities and what is needed for the shop. Typically requires extensive knowledge of specific programs or production lines.
Primary Duties & Responsibilities:
- Inventory Management: Contribute to the maintenance of accurate inventory records, conducting regular audits, cycle counts, and reconciliations to identify discrepancies, minimize inventory variances, and ensure inventory accuracy.
- Receive inventory via the ERP system
- Validate and verify documentation received matches parts and count quantity is correct. Return paperwork and parts to Receiving Inspection/Quality when discrepancies are found
- Inform Stock Room Supervisor when new parts are received and assist in establishing new inventory locations
- Fill back orders as required, issue out of the ERP system, deliver to proper work center
- Receive Job Orders to stock, verify all Bill of Material items have been issued to the work order and all operations have been closed, change status of Job order to “Complete”
- Overflow identification
- Verify all parts received are put in proper locations by close of business
- View production tickets in the ERP system in order to assist in the location of parts necessary to fulfill a back order
- Assist in issuing and processing basic assembly kits
- Assist with problem solving (lost and damage parts) and supports other departments as necessary
- Sign-off on job orders
- Assist in training new personnel for Stock Clerk and Material/Inventory Control I positions
- Assist Production Control Planners with various issues
- Verify Stock Clerk’s Bill of Material items are complete and accurate, issue all material items out of inventory to Job Orders, fill out Back Order Tickets as required and place on proper bins
- Increase Stock Room productivity by developing more efficient systems
- Work with Quality Personnel and identify non-conforming parts
- Keep stock in orderly arrangement
- Issue additional hardware to Job Orders as well as returns if not required
- Inform planner if hardware is required by assembly but not listed on the Bill of Material. Planner will get order red-lined by Engineering
- Close out Stock Rooms Operation on Job Orders
- Process complex assembly orders, verify parts are correct and coach personnel if corrections are required. Issue material out of inventory.
- Release Sub-Assembly and Assembly orders for various programs if Planners require assistance
- Inform production Control Planners and Assembly Supervision via e-mail if shortages exist on Assembly orders
- Informs appropriate Planners when minimum quantities are reached for re-order
- Prepares shortage documentation/fill out Back Order Tickets
- Interfaces with other functional areas such as Receiving Inspection, Production Control and Assembly departments in order to coordinate shortages or expedite stock problems
- Prioritize kits and carts to be pulled with stock room personnel. Make sure work trays have orders available. Coordinate with personnel on all shifts
- Assist Supervisor with tasks as needed. Able to review inventory transaction fields to find the root cause of problems and inaccuracies.
- Make corrections on stocking or issuing problems on orders when notified of a discrepancy
- Process flow knowledge of varying programs
- Instrumental in the training process of new Planners and Receiving Inspection Quality personnel
- Assist assembly personnel to verify the kits they require are pulled and available. Notify assembly planner if order needs to be released
- Process spare and OSW Job Orders
- Receives in purchased parts and fabricated parts from Receiving/Inspection department
- Package, organize, and place parts in proper stockroom location(s)
Required Skills:
- Must be a team player and have sound judgement
- Intermediate proficiency in Microsoft Office
- Good organizational skills
- Ability to work in a demanding fast-paced environment
- Demonstrate initiative and problem-solving skills to resolve and eliminate constraints
- Must possess strong verbal and written communication skills as well as strong interpersonal skills
- Read, write and understand the English language
- Must be able to work assigned schedule with minimal absences.
Experience & Education
- High school diploma or GED
- Minimum of 2 years of industry and company experience required
This requisition is closed to applications.