Operations Supervisor
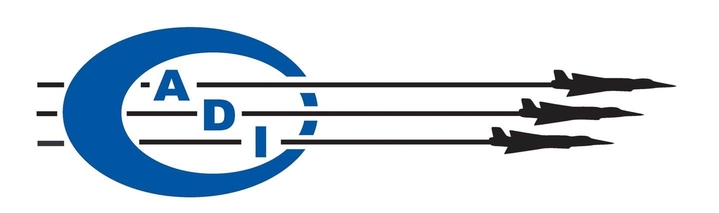
189
Precision Castparts Corp. (PCC) is a leading worldwide, diversified manufacturer of complex metal components and products. It serves the aerospace, power, and general industrial markets. PCC is the market leader in manufacturing large, complex structural investment castings, airfoil castings, and forged components used in jet aircraft engines and industrial gas turbines. The Company is also a leading producer of highly engineered, critical fasteners for aerospace and other general industrial markets, manufactures extruded seamless pipe, fittings, forgings, and clad products for power generation and oil & gas applications, and supplies metal alloys and other materials to the casting and forging industries. PCC is a high quality business with dominant positions in most segments of the markets in which it serves.
Headquartered in Portland, Oregon, this over 10 billion dollar company employs more than 29,500 people worldwide. PCC has over 160 plants and has a presence in twenty-six states in the US and in over a dozen countries. PCC is relentless in its dedication to being a high-quality, low-cost and on-time producer; delivering the highest value to its customers and shareholders while continually pursuing strategic, profitable growth.
Effective early February 2016, Berkshire Hathaway, led by chairman and CEO Warren E. Buffet, acquired Precision Castparts Corp.
PCC Aerostructures now includes more than 30 plants in the U.S, Europe and Asia with over 5500 employees and has ambitious growth plans. Businesses within PCC Aerostructures include Primus International, SPS Aerostructures, Centra, Avibank and AVK, Klune, ProCoat, Southwest United Industries, Progressive Incorporated, Noranco, Synchronous, and Kalistrut. Plants locations include Washington, Utah, California, Oklahoma, Kansas, Texas, Ohio, Canada, Mexico, the UK and China.
Aerospace Dynamics International, Inc. (ADI) manufactures machined parts and assemblies for the commercial and military aerospace industries. It offers structural components, caps, panels, bulkheads, fittings, longerons, spars, chords, wing ribs, thrust reversers, structural machine parts, manufacturing tooling and stretch form blocks.
ADI was acquired by PCC in April 2014. The company has received significant capital investments since the acquisition and has a highly positive growth trajectory ahead. Comprising seven facilities on its campus in Valencia, CA, ADI has over 300 full-time employees on staff.
The Operations Supervisor will supervise and coordinate activities of workers engaged in performing various processes on customer parts or products in a heavy manufacturing environment. This individual will deliver results in a multi-shift machining environment and will measure operational performance via metrics to meet the daily, weekly and monthly goals of production. The products are primarily aerospace components for commercial and military aircraft.
Understand, adhere, and demonstrate the company’s commitment to QUALITY and SAFETY!
Responsible for the performance improvement and discipline of the employees that report to them with the assistance of the Human Resource Department and the Operations Director.
Assists in the development and implementation of new or improved manufacturing methods, set-up reductions, productivity improvements, throughput improvements and variable cost improvements.
Meets with employees daily, reflecting on problems, solutions, and challenges; thereby creating a culture of continuous improvement and contributing towards becoming a learning organization.
Implements and coordinates cross training of department employees to insure the elimination of all skill gaps, resulting in a more skilled and adaptable workforce. Insures the completion of required competency forms and certifications, as well as maintains an employee skill matrix.
Instills and maintains a positive, can-do team atmosphere; holding regular team meetings, assigning team members’ tasks, and coordinating required support services needed. Uses area boards to ensure results.
Personally supervises the conduct of Root Cause Corrective Action working sessions when safety and quality escapes occur.
Reviews production orders or schedules to ascertain product data such as types, quantities, and specifications of products and scheduled delivery dates in order to plan department operations.
Executes manufacturing schedules and coordinates manufacturing activities to ensure production and quality of products meets specifications.
Reviews production and operating metrics and reports and resolves operational, manufacturing, and maintenance problems to ensure minimum costs and prevent delays.
Inspects machines and equipment to ensure specific operational performance and optimum utilization. Manages a pro-active Preventive Maintenance program.
Develops or revises standard operational and working practices and observes workers to ensure compliance with standards.
Ensures that proper tooling is available for all production machines and product lines; or that material is on hand for the creation or modification of necessary jigs and tooling.
Resolves employee suggestions and or complaints or submits unsettled employees issues for further action by Director of Manufacturing and Director of Human Resources where and when appropriate.
Maintains a clean and safe work place while executing the shop production schedule.
Responsible for the execution of the production schedule.
Ensures preventive maintenance is scheduled on faulty equipment
Communicates with Production Scheduling regarding shut downs and other factors that affect the scheduling of production.
Provides employee coaching and development. Ensures employees have a working knowledge of the machines they operate and the tools they use.
Verifies all paper work is completed in compliance with shop procedures.
Works with Human Resources to ensure safety program is followed. Performs accident investigations as needed.
3-7 years of Manufacturing Experience, preferably in aerospace or automotive industry
Bachelor’s degree in Engineering or a related discipline is preferred
MBA or MS is highly desirable
Previous experience in a heavy industrial environment is preferred
Knowledge of raw materials, production processes, quality controls, and costs
Understand/use techniques for effective control of delivered quality, cost, and schedule in the processing of aerospace products
Knowledge of management principles involved in strategic planning and forecasting including people, material, and equipment resource allocation; corporate and human resource policies and benefits; leadership; teaming; and production methods
Thorough knowledge of lean manufacturing work area practices including 5-S, Visual Controls, Standard Work, work center metrics, and continuous improvement processes and able to instruct others in these practices
Proactive communicator who can clearly articulate results and needs across all levels
Able to establish and communicate clear priorities and to influence others to support and act on those priorities
Proven ability to manage multiple projects with competing deadlines
Must have the knowledge, skill, and ability to meet expectations for required competencies in position, which includes: 1) safety, health, and environmental awareness, 2) business ethics and compliance, 3) technical/professional competence and quality & time management, 4) interpersonal relations and communication skills, 5) initiative, flexibility, innovation, and adaptability, 6) continuous improvement and problem solving, and 7) planning and organizing.
Ability to follow directions and follow all safety protocols.
A demonstrated ability to lead and coach others.
Strong interpersonal and communication skills
This requisition is closed to applications.